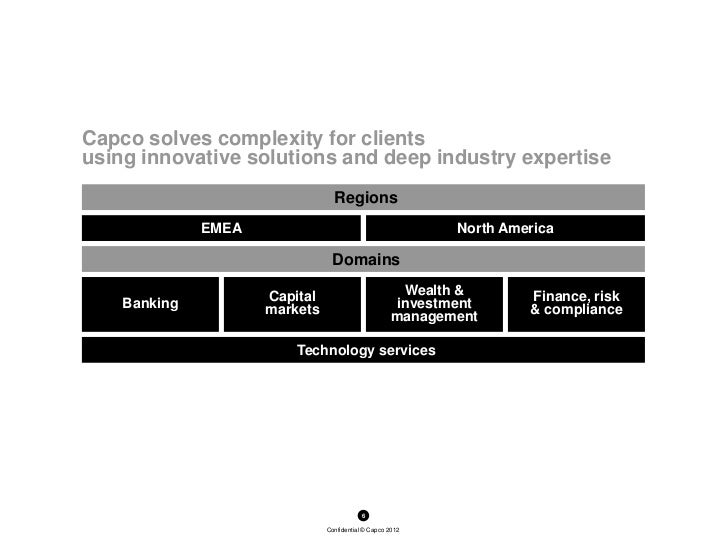
Production of Acetone Using Catalytic
Dehydrogenation of Isopropyl Alcohol
Instructions on use of Turton et al.’s Excel program CAPCOST. Clarkson University's Department of Chemical and Biomolecular Engineering. Disclaimer: The material on this page is intended for instructional purposes by Clarkson University students only. Some employers are moving away from offering traditional coverage with a provider network and instead are using reference-based pricing for some or all of services they cover. Under reference-based pricing, the employer (supported by a third party administrator TPA or other vendor) pays a set a price for each health care service instead of negotiating prices with providers. Capcost software, free download A built-in project calendar A scheduling module Ad hoc reporting tools Many advanced features Such as branching logic, file uploading, and calculated fields. A quick and easy software installation process So that you can get REDCap running and fully functional in a matter of minutes.
Project Leader: Mike TremouletVerify results shown in Example 2.14, p.68 of Text using CAPCOST program that came with the book. Compare with your numbers against the data given Table E2.15. Submit the first page (only) of the printout. Verify the cost of the pump P-l0lA using the cost correlation given in. Appendix A of Text.
Team Members: Mike Unton and Ed Feng
Ceng 403 - Equipment Design
October 11, 1998
Table of Contents:
- Preliminary Design
- Preliminary Reaction Side PFD
- Qualitative Explanation of Process
- Detailed Cost Data
- Discussion of Development of Enhancements
- Methods and Intent
- Role of Engineering Judgment
- Optimization and Trial Simulations
- Costing Methods
- Augmented Design
- Reaction Side PFD
- Changes from Base-Case Process
- Detailed Cost Data
1. Abstract
This design project employs Aspen to simulate the optimization of the reaction side of a catalytic dehydrogenation plant which produces acetone and hydrogen from isopropanol. Optimization was carried out on a preliminary base case design. The Net P resent Value of the expenditures required in this section of the plant to process 34.82 Kmol/h of isopropanol with an approximately 90% single-pass conversion was reduced by $973,000 or 15.2% of its original value, as estimated by CAPCOST. While the capit al cost of the project remained essentially constant, an 18.6% savings in yearly operating costs was realized. Salient features of this augmented design include the addition of an adiabatic reactor to the system, replacement of high pressure steam with mo lten salt and increased pressure in the process stream. These modifications allowed reduction in the size and heat duty of the heated reactor, elimination of costly high pressure steam and the removal of a refrigerated-water heat exchanger.
2. Introduction
Acetone is often produced as a by-product in the production of phenol. The cumene hydroperoxide generated in that process is cleaved to form phenol and acetone. Catalytic dehydrogenation of isopropanol can be chosen as an alternative synthetic rout e when high-purity acetone is required, such as in biomedical applications. Turton et.al. mentions that a single pass conversion of 85-92% with respect to isopropanol, with reactor conditions of 2 bar and 350° C, is generally ac hieved. A molten salt stream will be used a heat source for the endothermic reaction:
The acetone produced in the reactor passes into a phase separator and then into a separation system that includes one stripping and two distillation columns. A recycle stream takes a mixture of unreacted isopropyl alcohol and water, with a trace amount of acetone, back into a mixer that feeds the reaction system. Using the catalyst which will be employed throughout this analysis, the reaction is first order with respect to the concentration of isopropanol and has an Arrhenius dependence on temperature with E=72.38 MJ/kmol and k=351,000 cubic m gas/cubic m reactor sec.
3. Preliminary Design
3.1 Preliminary Reaction Side PFD
The authors of Turton et.al. present the Process Flow Diagram (PFD) in Figure 1 as a preliminary design. The production of acetone is 34.82 kmol/h from a process feed of 34.82 kmol/h of isopropanol, representing an overall conversion of approximate ly 100%. The reactor feed consists of this process feed plus a recycle stream with approximately 3.8 kmol/h of isopropanol. Table 1 lists information pertinent to the design of the individual units. Table 2 gives details about the compositions and states of the individual streams.
3.2 Qualitative Explanation of Process
The process may be qualitatively explained as follows. Fresh, azeotropic (88% by weight in water) isopropanol is mixed with the recycle stream from the separation side of the plant. The recycled isopropanol contains a trace amount of acetone. The c ontents of the mixer are fed to a pump that satisfies the pressure requirements of the reactor. The pump feeds a heat exchanger, E-401, which vaporizes the process stream using high pressure steam. The process stream then enters a multitube reactor heated by a molten salt stream. The heat transferred to the reacting gas stream is supplied by a fired heater to molten salt which is circulated by means of a centrifugal pump. The conversion of isopropanol to acetone and hydrogen takes place over a solid catal yst in the reaction tubes. The temperature in the reactor ramps up from 234° C to 350° C in the first quarter of the reactor which thereafter operates isothermally. The reacted stream must then be cool ed so the hydrogen can easily be removed. This is accomplished by means of two successive heat exchangers, the first taking away the heat from the stream with cooling tower water, the second with refrigerated water. The result is a stream at 20° C and 1.63 bar.
3.3 Detailed Cost Data
Capital cost details for this design are as follows.
Total Grass Roots Cost of Reaction Side: $1,006,000

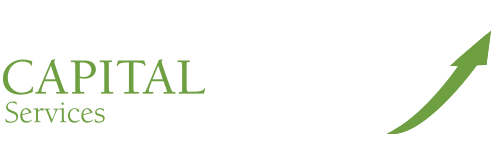
Reactor Bare Module: $204,300
R-401 $204,300
Heat Exchanger Bare Module: $96,500
E-401 $39,700E-402 $40,800
E-403 $16,000
Fired Heater Bare Module: $234,200
H-401 $234,200
Pump Bare Module: $73,100
P-401AB $26,400P-402AB $46,700
Vessel Bare Module: $9,600
V-401 $9,600
Bare Module Cost of Reaction Side: $617,700
Catalyst $68,200
HiTec Salt N/A
Operation Cost details for this design are as follows. (Based on 350 days operation per year)
Total Yearly Operating Cost: $496,100

Steam: $138,000
Natural Gas: $61,000
Cooling Water: $21,800
Electricity $1,500
Net Present Value of Expenditures: $6,382,000
(7% discount rate, 20 yr. project)
4. Discussion of Development of Enhancements
4.1 Methods and Intent
The goal of modifying this process is to reduce the Net Present Value of the expenditures required to produce 34.82 Kmol/h of isopropanol with approximately 90% single pass conversion. Constraints are to maintain the same process safety and environ mental responsibility, or to improve in these areas if the base case is found inadequate. Additionally, our design must not arrive at its savings by passing costs downstream. This implies that the streams leaving the phase separator must at least be as am enable to downstream processing as those found in the preliminary design. Chemical Engineering and Economic fundamentals as well as creative thinking and practical experience (where available) will be employed to achieve this goal.
4.2 Role of Engineering Judgment
As is often the case in 'real-world' chemical processing we were faced several times in this project with a lack of readily available, reliable data upon which to base our design. When we encountered this situation we made assumptions and approxima tions based on our engineering judgment. A good assumption was one which satisfied the question 'Does this make sense?' We believe that all of the assumptions and approximations presented in our final design are sound, inasmuch as they best we could do wi th the data at our disposal.
4.3 Optimization and Trial Simulations
Aspen is used as a simulation tool to find the optimal combination of equipment that minimizes base and operating costs. The design changes involve the replacement of some equipment with others, and the usefulness of Aspen is realized in simulating these changes. The use of several property packages intended to incorporate the effects of vapor-phase non-idealities was explored. For this purpose, the Peng-Robinson and Soave–Redlich/Kwong packages gave nearly identical stream data. Since most runs we re carried out using Peng-Robinson, the stream tables contained in this report are based on this property package. An ideal property package was employed for all liquid streams. The molten salt stream was not explicitly modeled in Aspen, due to a lack of physical property data for the salts. The reactor heat transfer was still modeled, however. A heat transfer coefficient of 60 W/m2K was used to model the transfer of heat from the molten salt to the reactor tubes. Runs were then performed to de termine the amount of heat transfer area required to satisfy the heating requirements of the process stream. (The heating requirements of the process stream may be calculated by adding the heat of reaction and the sensible heat needed to raise the tempera ture of the stream.) The temperature profile in the reactor resulting from the use of this heat transfer coefficient and its effect on required reactor size was determined by iteration in Aspen. It was found that given the reactor volume needed to accompl ish the desired conversion and the flowrate of salt in Turton, et. al., one inch was the maximum diameter for the reactor tubes. Throughout the design process we imposed the additional constraint that the stream leaving the phase separator be similar in t emperature and pressure to the one in the preliminary design offered in Turton et. al. This was one method of ensuring that savings realized in our design did not come at the expense of units downstream.
4.4 Costing Methods
The program CAPCOST was used to price the pieces of equipment employed in this design, as well as in the preliminary design. Since 'heated reactor' is not a CAPCOST option, this unit is costed as though it was a floating head shell-and-tube heat ex changer because it appears to be similar in design to this type of equipment. 'Adiabatic reactor' is also not a CAPCOST option, so it is costed as a vessel because it is simply a catalyst-filled tube. The mixing vessel, fired heater, pumps and heat exchan gers were available options in CAPCOST and were costed with the appropriate materials of construction for the conditions of the process stream. Utilities and labor costs were used as given in Turton, et. al.
5 Augmented Design
5.1 Reaction Side PFD
The authors of this paper present the PFD shown in Fig. 2. The production of acetone is 34.82 kmol/h from a feed of 34.82 kmol/h of isopropanol, representing an overall conversion of approximately 100%. Table 3 lists information pertinent to the design of the individual units. Table 4 gives details about the compositions and states of the individual streams.
5.2 Changes from Base-Case Process
Unless otherwise noted in this paragraph, the process conditions and equipment used in the augmented design are very similar or identical to those in the base case process described in Sec. 3.2. The first change effected was to increase pressure in the reactor. This change was made in order to increase reaction rate as well as to keep the composition of the phase separator outlet the same as in the base case. This resulted in a need for a larger pump to feed the reactor. The feed vaporizer, E-401, now uses molten salt to vaporize the process stream, rather than using high pressure steam. This change was made because high pressure steam is more costly per GJ of heating than the natural gas used in the fired heater. There are large capital expenditur es to install a fired heater, but the marginal cost of increasing the size of this type of unit is a low percentage of total cost. Therefore, since a fired heater is already required for this process, we opted to reap the benefits of the lower-cost natura l gas by increasing the capacity of the fired heater. The flowrate of the molten salt was scaled up as a linear function of the heat duty, and the salt pump resized accordingly. The heat transfer and concomitant temperature profile in the multitube reacto r were modeled as described in Sec 4.3. The temperature in the reactor ramps up from 234° C to 350° C in the first quarter of the reactor, which thereafter operates approximately isothermally. The reac ted stream must then be cooled so that the non-condensable hydrogen can easily be removed. This is partially accomplished in a catalyst-charged adiabatic reactor in series with the heated reactor. The additional reaction that takes place brings the single -pass conversion up to approximately 90%. The adiabatic reactor was added for the 'free cooling' of the endothermic reaction and the accompanying reduction in duty on the fired heater. Chart 1 shows the temperature profile of the reacting stream across bo th reactors. The process fluid is then condensed and cooled in a heat exchanger using cooling tower water. The result is a stream at 45° C and 4.65 bar. The heat exchanger that used refrigerated water as a coolant was removed fr om the design to reduce capital costs and to eliminate dependence on the costly refrigerated water. The operation of the phase separator with respect to the composition of the outlet streams is unchanged from the base case because the additional pressure compensates for higher temperature. (i.e. the same amount of acetone is in the feed to the absorber.)
5.3 Detailed Cost Data
Capital cost details for the augmented design are as follows.
Total Grass Roots Cost of Reaction Side $1,031,000
Percent Savings over Base Case: -2.4%
Reactor Bare Module: $122,700
R-401 $104,400R-402H $18,300
Heat Exchanger Bare Module: $80,500
E-401 $39,700E-402 $40,800
Fired Heater Bare Module: $360,000
H-401 $360,000
Pump Bare Module: $93,900
P-401AB $34,300P-402AB $59,600
Vessel Bare Module: $9,600
V-401 $9,600
Bare Module Cost of Reaction Side: $666,700
Catalyst $19,900
HiTec Salt N/A
Operation Cost details for this design are as follows. (Based on 350 days operation per year)
Total Yearly Operating Cost: $404,000
Percent Savings over Base Case: 18.6%
Labor: $273,800Steam: $0
Natural Gas: $122,400
Cooling Water: $4,700
Electricity: $3,100
Net Present Value of Expenditures: $5,409,000
(7% discount rate, 20 yr. project)
Total Savings over Base Case: $973,000
Percentage Savings over Base Case: 15.2%
6. Conclusions
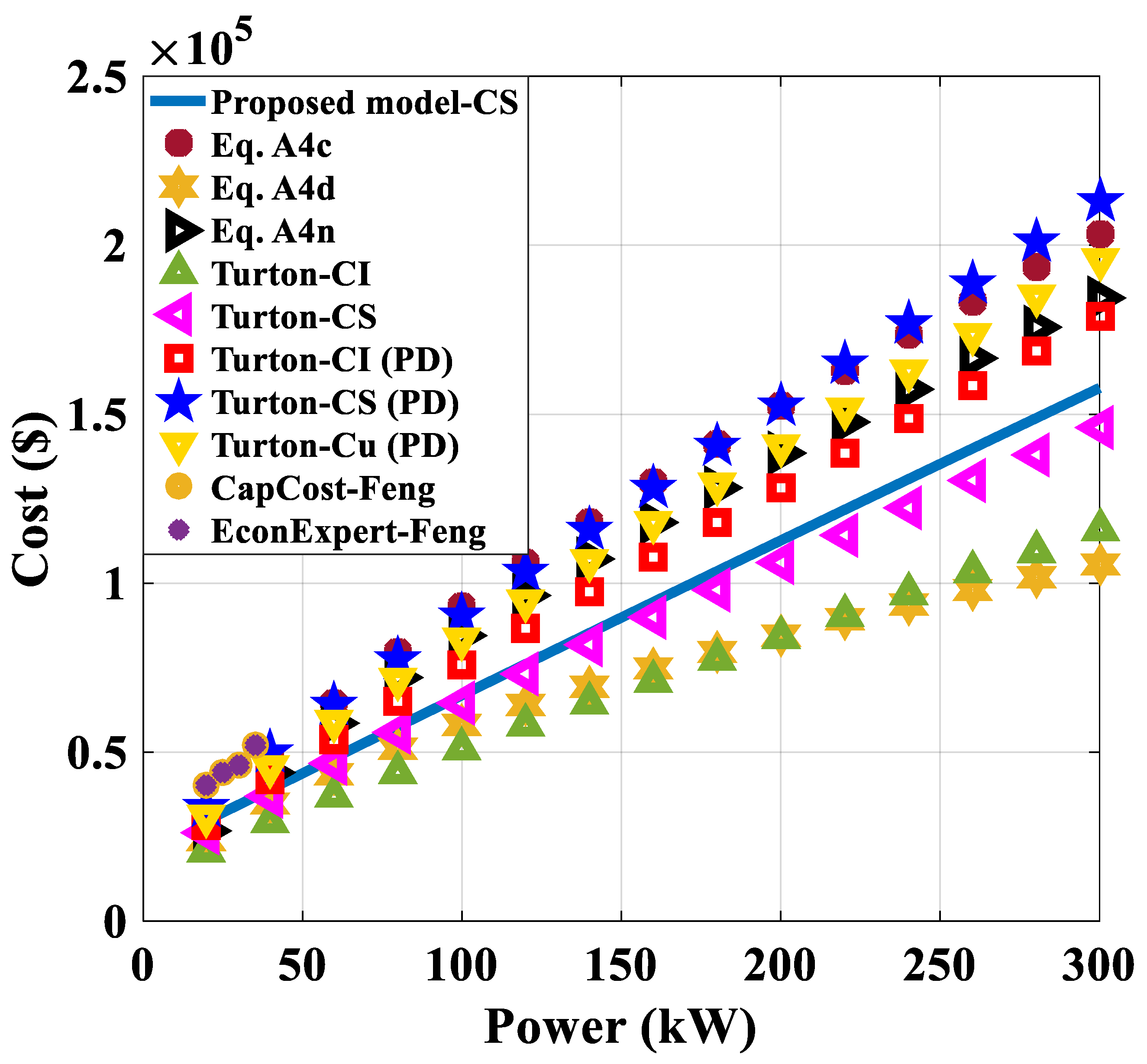
The new design offers economic benefits in the overall costs of the reaction side of the plant. In changing the plant design by incorporating two reactors instead of one, $81,600 is saved through the reduced volume of the heated reactor and the sim ple nature of the adiabatic reactor. The second reactor eliminates the need for one of the two heat exchangers used in the preliminary design, which saves an additional $16,000. The new system of reactors also decreases the required catalyst volume, which offers an addition $48,300. This design change results in a need for a higher capacity in the fired heater and the centrifugal pumps though, which increases the base cost of these items by $146,600. Overall, the base cost of the new design is $25,000 gre ater than the preliminary design, an increase of 2.4%.
The operating cost savings is the main benefit of these design changes and reduces the overall cost of the reaction side of the plant. Nearly $138,000 is saved yearly because the new design does not require steam, while it only results in a $45,900 inc rease in other costs such as natural gas, cooling water and electricity. The yearly reduction of $92,100 in operating costs, an 18.6% savings, more than compensates for the minimal increase in base cost.
7. References
1. Kirk-Othmer: Encyclopedia of Chemical Technology, 3rd Edition, vol. 1, 179-191, John Wiley and Son, 1976.
2. Encyclopedia of Chemical Processing and Design, Ed. J. J. McKetta, and W. A. Cunningham, vol. 1, 314-362, 1976.
3. Analysis, Synthesis and Design of Chemical Processes, R. Turton, R. Bailie, W. Whiting and J. Shaeiwitz, Prentice-Hall, 1988.
Fig. 1: Preliminary Acetone Production PFD (Reactor Side
Table 1: Equipment Used in Preliminary Process
Equipment | V-401 | R-401 | Equipment | P-401AB | P-402AB |
MOC | Carbon Steel | Carbon Steel | MOC | Carbon Steel | Carbon Steel |
Diameter (m) | 0.80 | 1.85 | Power (kW) | 0.43 | 2.53 |
Height/Length (m) | 2.40 | 8.0 | Efficiency | 0.4 | 0.5 |
Equipment | H-401 | E-401 | E-402 | E-403 |
MOC | Carbon Steel | Carbon Steel | Carbon Steel | Carbon Steel |
Heat Duty (MJ/h) | 2906 | 3550 | 3430 | 414 |
Area (m^2) | 40.5 | 70.3 | 77.6 | 8.5 |
Fig. 2: Augmented Acetone Production PFD (Reaction Side)
Table 2: Equipment Used in Augmented Process
EquipmentR-401 | R-402H | Equipment | P-401AB | P-402AB | ||
MOC | Carbon Steel | Carbon Steel | Carbon Steel | MOC | Carbon Steel | Carbon Steel |
Diameter (m) | 0.8 | 0.9 | 0.91 | Power (kW) | 1.0 | 5.06 |
Height/Length (m) | 2.4 | 8.0 | 3.81 | Efficiency | 0.4 | 0.5 |
Equipment | H-401 | E-401 | E-402 |
MOC | Carbon Steel | Carbon Steel | Carbon Steel |
Heat Duty (MJ/h) | 5826 | 3550 | 3226 |
Area (m^2) | 91.0 | 70.3 | 77.6 |
Table 3: Individual Stream Flows for Preliminary Design
Stream ID | 1 | 2 | 3 | 4 | 5 | 6 | 7 | 8 | 10 | 20 |
From | V-401 | P-401AB | E-401 | R-401 | E-402 | E-403 | R-401 | H-401 | ||
To | V-401 | P-401AB | E-401 | R-401 | E-402 | E-403 | V-402 | P-402AB | R-401 | V-401 |
Phase | LIQUID | LIQUID | LIQUID | LIQUID | VAPOR | MIXED | MIXED | LIQUID | LIQUID | LIQUID |
HYDROGEN (Kmol/h) | 0.0 | 0.0 | 0.0 | 0.0 | 34.78 | 34.78 | 34.78 | 0.0 | 0.0 | 0.0 |
ACETONE (Kmol/h) | 0.0 | 0.162 | 0.162 | 0.162 | 34.94 | 34.94 | 34.94 | 0.0 | 0.0 | 0.162 |
IPA (Kmol/h) | 34.82 | 38.47 | 38.47 | 38.47 | 3.69 | 3.69 | 3.69 | 0.0 | 0.0 | 3.65 |
WATER (Kmol/h) | 17.14 | 19.04 | 19.04 | 19.04 | 19.04 | 19.04 | 19.04 | 0.0 | 0.0 | 1.9 |
Total Flow (kmol/h) | 52.0 | 57.7 | 57.7 | 57.7 | 92.5 | 92.5 | 92.5 | 35.1 | 35.1 | 5.7 |
Temperature (C) | 25.0 | 31.1 | 31.2 | 31.2 | 350.0 | 45.3 | 20.4 | 357 | 407 | 83 |
Pressure (Bar) | 1.01 | 1.01 | 2.3 | 2.3 | 1.91 | 1.77 | 1.65 | 2.66 | 3 | 1.2 |
Vapor Frac | 0.0 | 0.0 | 0.0 | 1.0 | 1.0 | 0.49 | 0.41 | 0.0 | 0.0 | 0.0 |
Stream ID | 8 | 9 | 10 | RW-1A | RW-1B | CW-1A | CW-1B | HPS-1A | HPS-1B |
From | R-401A | P-402AB | H-401 | E-403 | E-402 | E-401 | |||
To | P-402AB | H-401 | R-401A | E-403 | E-402 | E-401 | |||
Phase | LIQUID | LIQUID | LIQUID | LIQUID | LIQUID | LIQUID | LIQUID | VAPOR | LIQUID |
WATER (Kmol/h) | - | - | - | 4857 | 4857 | ||||
MOLTEN SALT(tonne/h) | 35.1 | 35.1 | 35.1 | - | - | - | - | - | - |
Temperature (C) | 357 | 357 | 407 | 5.0 | 15.0 | 30.0 | 40.0 | 254 | 253.3 |
Pressure (Bar) | 1.0 | 3.0 | 2.66 | 1.0 | 1.0 | 1.0 | 1.0 | 42 | 2.16 |
Capcost Program Login
Table 4: Individual Stream Flows for Augmented Design
Stream ID | 1 | 2 | 3 | 4 | 5 | 6 | 7 | 20 |
From | V-401 | P-401AB | E-401 | R-401 | R-402H | E-402 | ||
To | V-401 | P-401AB | E-401 | R-401 | R-402H | E-402 | V-402 | V-401 |
Phase | LIQUID | LIQUID | LIQUID | VAPOR | VAPOR | VAPOR | MIXED | LIQUID |
HYDROGEN (Kmol/h) | 0 | 0 | 0 | 0 | 27.77 | 34.77 | 34.77 | 0 |
ACETONE (Kmol/h) | 0 | 0.163 | 0.163 | 0.163 | 27.93 | 34.93 | 34.93 | 0.163 |
IPA (Kmol/h) | 34.82 | 38.3 | 38.3 | 38.3 | 10.53 | 3.53 | 3.53 | 3.48 |
WATER (Kmol/h) | 17.14 | 19.03 | 19.03 | 19.03 | 19.03 | 19.03 | 19.03 | 1.89 |
Total Flow (kmol/h) | 51.96 | 57.493 | 57.493 | 57.493 | 85.26 | 92.26 | 92.26 | 5.533 |
Temperature (C) | 25 | 30.9 | 31.3 | 234 | 350 | 285.6 | 45.1 | 83 |
Pressure (Bar) | 1.01 | 1.01 | 5.3 | 5.2 | 4.85 | 4.75 | 4.65 | 1.2 |
Vapor Frac | 0 | 0 | 0 | 1 | 1 | 1 | 0.42 | 0 |
Stream ID | S1 | S2 | S3 | S4 | S5 | S6 | S7 | CW-1A | CW-1B |
From | H-401 | B6 | B6 | E-401 | R-401 | B7 | P-402AB | ||
To | B6 | E-401 | R-401 | B7 | B7 | P-402AB | H-401 | ||
Phase | LIQUID | LIQUID | LIQUID | LIQUID | LIQUID | LIQUID | LIQUID | ||
WATER (Kmol/h) | - | - | - | - | - | - | - | ||
MOLTEN SALT(tonne/h) | 70.4 | 70.4 | 70.4 | ||||||
Temperature (C) | 407 | 407 | 407 | 357 | 357 | 357 | 357 | ||
Pressure (Bar) | 2.66 | 2.66 | 2.66 | 1 | 1 | 1 | 3 |
Chart 1: Temperature Profile for Augmented Design
Capcost Program Application
iTemp = roundAmount(lCp)
Range('userAddedExchangers').Select
ActiveCell.Offset(iSelection, 7).Value = '=ROUND(' & _
(lCp / Range('CEPCI')) & '*CEPCI, ' & iTemp & ')'
ActiveCell.Offset(iSelection, 7).Style = 'Currency'
ActiveCell.Offset(iSelection, 7).NumberFormat = _
'_($* #,##0_);_($* (#,##0);_($* '-'??_);_(@_)'
Can anyone help me, please?